Архив
Под маркой высокого качества
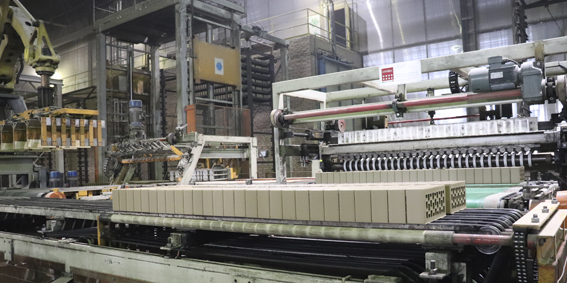
Недавно один из крупнейших производственных комплексов Сибири – ККЗ «Копыловская керамика» (с 2022 г. он входит в состав группы компаний FURBAU, занимается производством крупноформатных поризованных блоков и лицевого керамического кирпича) в рамках сотрудничества с Центром поддержки экспорта НО «Фондом развития бизнеса» принял участие в XXI международной специализированной выставке строительной индустрии KyrgyzBuild 2024 в Бишкеке (Кыргызстан). Эта рабочая поездка способствовала, в том числе, дальнейшему продвижению продукции предприятия за рубежом – качественные стройматериалы неизменно востребованы повсюду.
Строим дома на века
– Выставка в Кыргызстане входит в пятерку крупных престижных выставок по строительству в Центрально-Азиатском регионе, в 2024 году экспозиция объединила более 100 компаний из 15 стран. ККЗ представил свою продукцию на индивидуальном стенде как победитель регионального конкурса «Экспортер года – 2023» при взаимодействии с Центром поддержки экспорта НО «Фондом развития бизнеса» – пояснила Ольга Иванова, управляющий ООО ККЗ.– Наша поездка была успешной. И это, конечно, не случайно – Копыловский завод славится безупречным качеством. Продукция, которую он производит, отгружается в различные точки страны – от Владивостока до Краснодара, а также в Казахстан, Монголию, Киргизию. Серьезный объем потребляет Красноярский край, а также Новосибирск, Омск, Тюмень. На рынке Томской области еще 2 года назад оставалось лишь 10 % продукции, а вот за 2023 год, со вступлением ККЗ в группу компаний FURBAU, этот показатель вырос до 30 %, так как для руководства холдинга присутствие предприятия на местном строительном рынке – ключевой приоритет. Спрос на крупноформатный поризованный камень и кирпич возрастает. Стройматериалы, изготовленные под маркой ККЗ, отвечают стандартам ГОСТ 530-2012, что гарантирует их отличные потребительские свойства, а это всегда ценится клиентами.
Качественные строительные материалы – залог того, что здания любого назначения будут комфортными в эксплуатации и долговечными. Об этом мечтают все домовладельцы.
– Продукция высококлассная, – поделился Роман Н., томич (свою фамилию он попросил не называть). – Лично убедился в этом, когда несколько лет назад строил загородный дом. Дизайн фасада (мы использовали при облицовке кирпич двух цветов) – предмет нашей семейной гордости. Уверен, что коттедж «проживет» долго, правнуки нам за него спасибо скажут!
Лицевой керамический кирпич с модифицированной фактурной и ангобированной поверхностью, современные керамические стеновые блоки – вся линейка изделий пользуется спросом. С начала 2000-х годов на Копыловском заводе выпускают цветной кирпич, который потребители ценят как материал для облицовки зданий. Палитра разнообразна, включает красный, бежевый, серый, белый цвета, а также «шоколад», «сливки», «бронзу», «ваниль» – всех не перечислить.
Крупноформатные поризованные блоки зачастую называют «теплой керамикой»: стены из него прекрасно сохраняют тепло, позволяя снизить расходы на отопление здания. Их широко используют как в частной застройке, так и при возведении промышленных объектов, административных зданий. Так, в Томской области по этой технологии построена школа в с. Вершинино, в Новосибирске – целый квартал общей площадью 200 000 кв.м жилья возводит федеральная строительная компания «Брусника». В Красноярске блоки «родом» из Копылова применили при возведении объектов Универсиады – 2019. Популярен этот стройматериал и в Приморском крае.
Бережливые технологии - составляющая качества
На ККЗ качество обеспечивают благодаря нескольким составляющим. Например, наличию собственной сырьевой базы. Предприятие имеет карьерное хозяйство, где добывается сырье для производства – красножгущаяся и беложгущиеся глины.
Огромное значение имеет работа аккредитованной лаборатории качества и ОТК: данные службы исследуют сырье и готовую продукцию на всех этапах производства, начиная с момента добычи глины. Брак, таким образом, исключается.
Еще одна важнейшая составляющая – современное высокотехнологичное оборудование. Завод в 2010 году запустил новую промышленную линию итальянского производства. Сейчас принято решение дополнительно установить в отделении подготовки сырья прогрессивное перерабатывающее оборудование. Воплотить планы в реальность предполагается в ближайшее время.
Отличительная особенность производства на ККЗ – две особые установки. Ангобирующая установка позволяет наносить декоративное жидкое покрытие на поверхность облицовочного кирпича. Оно придает изделиям особую прочность и долговечность. Установка рустикатор предназначена для нанесения сухих декоративных покрытий.
На ККЗ стараются соответствовать последним тенденциям строительной «моды». Благодаря этому в номенклатуре завода появился гладкий лицевой кирпич Флеш из натуральной глины и песка. Его расцветка уникальна. В одной партии могут быть кирпичи от красного до почти черного цвета. При использовании технологии флеш-обжига на кирпиче происходит дополнительный поверхностный обжиг, который и обеспечивает переход цвета.
Наконец, завод с 2023 года внедряет у себя бережливые технологии в рамках нацпроекта «Производительность труда». В настоящее время пройден первый этап «пилота».
– Мы считаем, что это очень важный и нужный проект, который позволяет найти на предприятии внутренние резервы и сократить затраты без привлечения больших инвестиций благодаря применению инструментов бережливого производства. Эксперты регионального центра компетенций (РКЦ) определили эталонный участок, провели диагностику, нашли возможности для повышения производительности и качества продукции, создали инфоцентр, – отметила, в частности, Ольга Иванова, добавив, что участие в проекте продолжится.
В свою очередь, в РЦК рассказали: по итогам внедрения пилотного проекта по повышению производительности труда на заводе удалось снизить временные затраты с 13,3 до 11,7 часа, сократить объемы незавершенного производства с 163,9 до 143,2 тыс. шт., увеличить выработку на одного человека с 7500 до 8800 шт. кирпича в час. Показатели говорят сами за себя.
Как «вкалывают» роботы
На ККЗ выпускают свыше 40 видов изделий. Технологические линии автоматизированы, контроль за выполняемыми операциями производится с помощью программного обеспечения, разработанного сотрудниками завода.
– Проектная мощность линии составляет 60 млн условных штук изделий в год, – сообщил Марат Баранчин, начальник производства ККЗ. – Завод производит крупноформатные керамические пустотелые блоки и лицевой керамический кирпич формации 0,5–0,7 на одном и том же оборудовании и с небольшой его переналадкой.
Как «рождается» знаменитый кирпич под маркой ККЗ? Этапов его производства несколько. Все они требуют от специалистов, задействованных в процессе, и опыта, и внимания. Контроль над производством осуществляется строго круглосуточно, в мониторинге задействованы главный технолог, начальник ОТК, дежурные операторы и все заводские службы жизнеобеспечения. Ответственность за результаты труда коллективная.
Начинается все с подготовки шихты. Чтобы получить на выходе продукцию, отвечающую современным требованиям качества, все составляющие, применяемые в производстве, сначала проходят тщательный контроль на соответствие установленным нормативам ГОСТ 530-2012. Для создания запаса глины и песка на заводе предусмотрен крытый склад сырья, разделенный на отсеки, заполнение которых обеспечивает запас для бесперебойной работы завода в течение трех месяцев. В роли выгорающей добавки при производстве поризованных блоков применяются предварительно подготовленные древесные опилки.
Уникальное оборудование по переработке сырья позволяет подготавливать шихту для разных видов продукции. В начале сырье проходит через гладкие вальцы тонкого помола затем поступает в вертикальный смеситель (гомогенизатор), а дальше смесь подается к прессовому агрегату. Доувлажнение до необходимой формовочной влажности производится в смесителе-дегазаторе, где шихта продавливается через особые решетки (эта процедура дополнительно улучшает ее однородность перед подачей в экструдер). Затем масса должна побывать в вакуумной камере. При выходе из экструдера смесь продавливается через фильеру, конструкция которой придает изделиям требуемый профиль.
Формование и нарезка бруса на заготовки происходит в автоматическом режиме двумя системами резки для получения желаемого типа изделий, после чего огромный робот-манипулятор выверенными движениями укладывает заготовки на полки сушильной вагонетки.
– Процесс формовки автоматизирован, но это не означает, что люди в нем не заняты. Рабочие с помощью пультов управления наблюдают за показаниями датчиков температуры, скоростями, давлением, электронагрузкой на двигатели. Транспортеры снабжены металлодетекторами. Если вдруг в сырье обнаружится случайно металл, транспортер обязательно остановится автоматически. Это позволяет не повредить оборудование, – рассказал Марат Баранчин. – Точно так же действует оператор пульта пресса. Линию обслуживают два человека.
Сушка – не менее ответственный этап. Сушилка загружается автоматически, постепенно и равномерно. Вместительные вагонетки (к примеру, на одной умещается одновременно 2160 сырых кирпичных изделий) проходят «сырой» туннель ожидания, и далее – зоны с разной температурой и влажностью. Цикл сушки различных типов продукции занимает до 168 часов. Для обеспечения высокого качества отделение спроектировано в виде туннеля непрерывного действия. Транспортировка вагонеток также происходит в автоматическом режиме. В туннельной сушилке помещается 197 вагонеток с изделиями, или около 500 тыс. условных единиц продукции.
Обжигаем по правилам
После сушки изделия автоматически разгружаются с полок и направляются на линию укладки на печные вагонетки, чтобы уехать на обжиг. Этот этап благодаря наличию высоких температур и сложных механических режимов является самым ответственным в производстве. Он состоит из процедуры предварительного нагрева, обжига и охлаждения.
Печь обжига, длина которой составляет 168 м, а ширина канала 7 м, оснащена точечными высокоскоростными газовыми горелками, стационарными контрольно-измерительными приборами, системой автоматики подачи и горения топлива и поддержания заданного температурного режима печи с помощью компьютерной системы управления – показатели контролируют операторы. Для каждого вида изделий существует своя программа обжига.
После обжига готовые изделия автоматически разгружаются с печного вагона. Современная автоматизированная линия упаковки позволяет укладывать продукцию на поддоны ровными рядами, прокладывая их бумагой – это нужно для того, чтобы исключить вероятность образования потертостей на лицевой стороне кирпича при транспортировке. Каждый поддон с кирпичной продукцией упаковывается в пленку. Хранятся поддоны на складе готовой продукции отдельно по видам и маркам.
Конечно, в одной статье о солидном предприятии с историей нельзя затронуть все стороны его жизнедеятельности. Здесь чтут ветеранов и готовы обучать молодежь, прекрасно понимая, что искусственный интеллект не сможет полностью заменить человеческое участие. Сотрудничает завод с профильными вузами – например, с НИ ТПУ. Изучение технологий керамических материалов различного назначения является здесь одной из специальных дисциплин курса бакалавриата по основной образовательной программе «Химическая технология керамических и композиционных материалов» в рамках направления «Химическая технология». Студенты политеха, побывавшие на экскурсии на ККЗ, получают, таким образом, возможность лично увидеть все то, что изучали теоретически. И, безусловно, остаются очень довольны.
Планов у предприятия много, но озвучивать их пока преждевременно. Чем еще удивят производственники рынок строительных материалов? Это мы, потребители и ценители подлинного качества, вскоре узнаем!
Валерия ЗОЛОТУХИНА.